Staff and Alumni Use 3D Printing to Help Fight the Spread of COVID-19
April 17, 2020
Hillary Hempstead
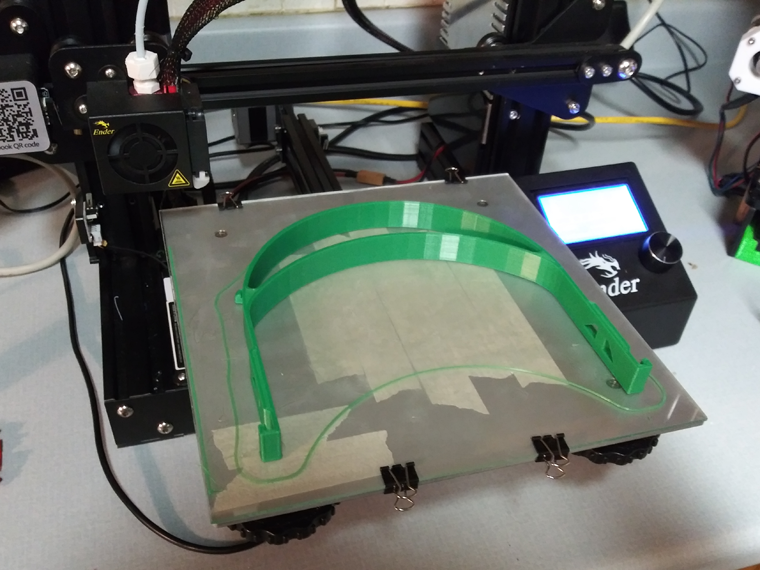
College staff and alumni are part of a growing number of individuals and entities using 3D printers to make personal protective equipment (PPE) for health care workers and others on the frontline of the COVID-19 pandemic.
Computer System Administrator Chris Mohler is no stranger to the world of 3D printing. During Winter Term 2019, Mohler even led 3D-Printing 101 with Cooper International Learning Center staff member Abe Reshad.
But suffice it to say, it’s not likely that Mohler foresaw running a 3D printing operation out of his home to produce components for much-needed personal protective equipment (PPE) for medical professionals.
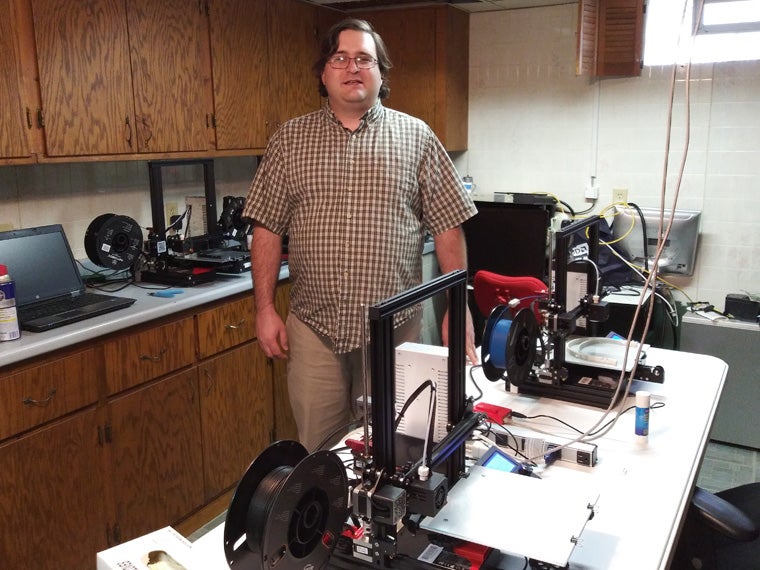
“There have been a lot of challenges involved in this project, and it's really pushed me—and these printers—to the limit,” says Mohler, who is running a fleet of eight printers from his basement to churn out approximately 30 headbands, daily. One printer is Mohler’s own, and the others are on loan through Reshad in the Cooper International Language Lab.
Through efforts led by Lorain County Community College (LCCC) and its Fab Lab , staff at Oberlin have partnered to print the headband component of the face shields used by healthcare workers and others on the frontlines of the pandemic. The headbands are then delivered to the Lorain County Office of Emergency Management and Homeland Security for distribution.
Mohler emphasizes that this is a joint effort that relies on a number of Oberlin staff, including Fabrication Lab supervisor Rachel Smith, who is also 3D printing headbands at her house, Jackie Fortino, who has sourced the PLA plastic filament used in printing and also does assembly, and Angela Szunyogh, who delivers the headbands to LCCC.
“It really is a team effort even though we are socially distancing and working from physically different areas, says Mohler. “It’s been fun dropping off the finished headbands at the college and then coming back a few days later to pick up the tote and find it’s filled with more 3D printing supplies.”
Mohler says that he hopes this small effort can make a difference and inspire others to help. “I'm hoping that this effort ultimately saves lives by keeping doctors and nurses safe so they can help those who are sick with COVID-19. I also hope this project inspires others to try and help—even small efforts can make a big difference.”
Alumni Find New Use for 3D Printer
Lenore Braford ‘07, founder of Piedmont Farm Animal Refuge in Pittsboro, North Carolina, and husband Paul Drake ‘07, are using a 3D printer typically used to prototype prosthetics for rescued animals to instead create PPE for medical workers.
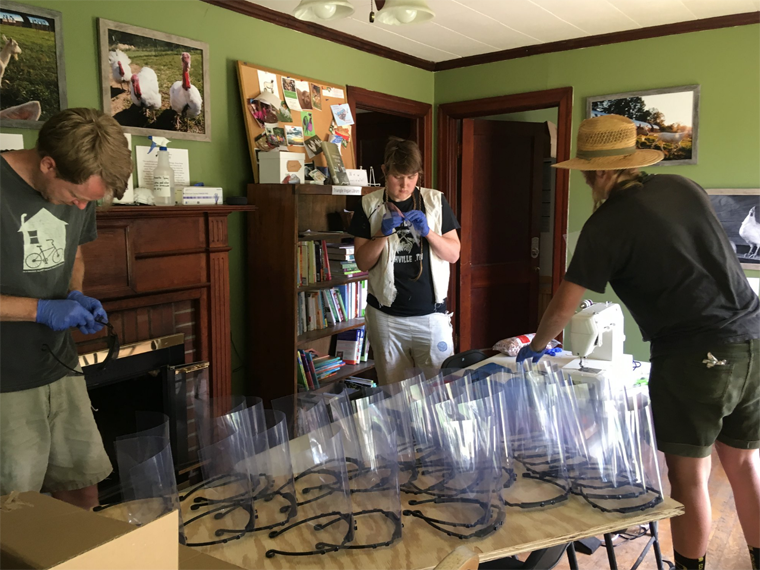
Photo credit: Courtesy of Lenore Bradford ‘07
“It’s easy to feel helpless against such an invisible threat as a virus,” says Bradford. “Having a goal of producing face shields helps us feel that we are contributing.”
Bradford, Drake, and a group of farm volunteers are printing headbands for face shields and also creating face shields made with clear binding covers and a hole puncher. The components are sanitized and boxed up for use at Duke Regional Hospital, Duke VA Hospital, Laurels Senior Care Center, and other nearby locations including a funeral home, an emergency dentist, and an emergency veterinary clinic.
“Our time at Oberlin instilled the idea that every single person can make a positive difference in our world by the actions they take each day,” says Bradford. “That goes for how we treat our animal friends as well as how we will get through this pandemic. We are remaining positive and we know that together we will make it through this.”
Artist Alum Turned Face Shield Assembler
Artist Damon Hamm ‘95 typically works to create metal sculpture in the shared makerspace Fat Cat Fab Lab in New York City’s West Village. Now he’s helping to create personal protective equipment for local hospitals.
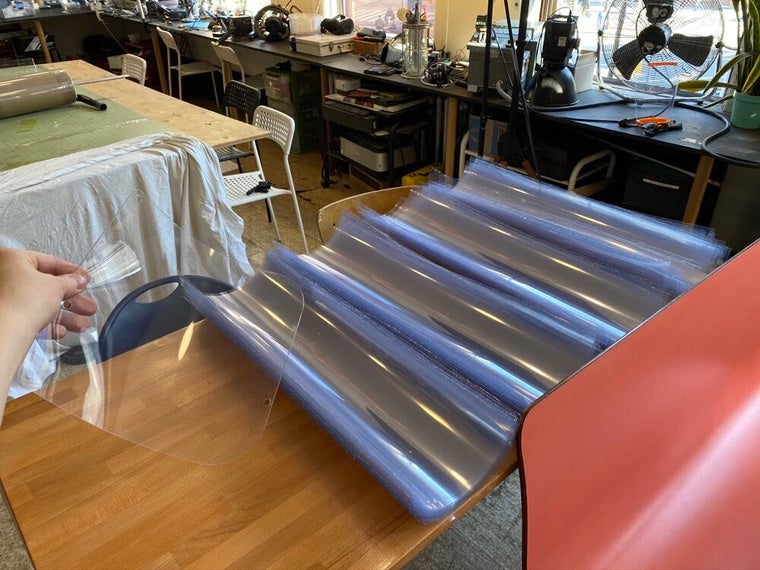
Photo credit: Courtesy of Damon Hamm
“When I arrived at the makerspace on March 20, I saw two other members in the middle of what looked like a huge project. They heard about the lack of PPE in the hospitals and decided to do whatever they could. It was for such a good cause, I couldn't resist helping.”
The group of makers Hamm works with is creating two versions of the face shields: one that is 3D printed, and another that is hand assembled. The group has also repurposed an industrial roll of food-grade biodegradable plastic that was originally used for thermoforming take out food containers and transformed it into face shields.
Since beginning the efforts, they’ve teamed up with several other makerspaces in the area and formed a coalition called nycmakesppe.com to share information and resources. They have also used donations to replenish their supply of raw materials and increase production capacity.
As of April 16, 2020, the coalition has delivered nearly 17,000 items of PPE in the New York City area.
Tags:
You may also like…
Omar Tells His Story
October 11, 2024
This December, Oberlin will present a concert version of Rhiannon Giddens’ award-winning opera, both at Finney Chapel in Oberlin and the Maltz Performing Arts Center in Cleveland. Surrounding it are all kinds of cross-disciplinary events for campus and community.
Historian Jennifer L. Morgan ’86 Wins MacArthur Fellowship
October 1, 2024
Specialist in early American slavery has earned acclaim for extensive research and writing on the subject.
Rhiannon Giddens to Deliver Commencement Address to Class of 2024
April 10, 2024
Grammy-winning musician and Oberlin alum will receive an honorary doctorate.